インフォメーション
朝活100本ノック /生産計画・在庫管理改革:76日目【在庫は「最悪のムダ」という考え方だけで良いのか?】
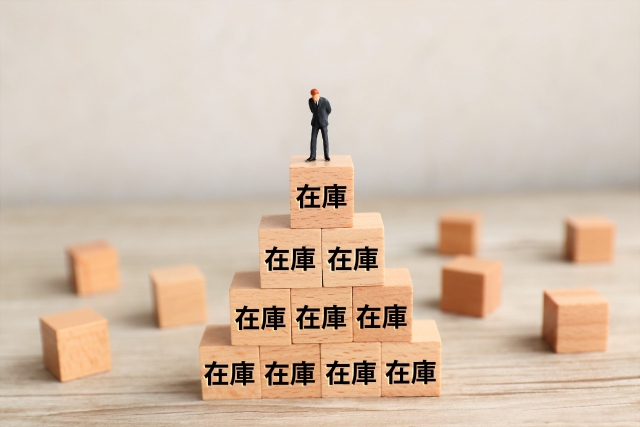
トヨタ生産方式「生産現場の7つのムダ」の「最大のムダ」は『在庫』
⇒在庫を減らすことが、「絶対的な善」となってきた
在庫の発生原因別では、在庫が一概に悪いと考えるのも無理がある!
「見越し在庫」は、サプライチェーンを上手にコントロールした証でもある
例・安全在庫:需要のばらつきに対応、設備故障や製品不良の内部からの変動への対応し、欠品による販売を止めない状態を作る。
黒字倒産が横行した1990年代の時から時代はリスクへの対応が必要となり、「在庫のムダ」という戒めの本質を冷静に見極めなければならない
業界、企業の年齢や体力、世界情勢などにより在庫の概念は全く違ったものになる。
何も考えずに、「在庫はムダ」と言った概念だけで進むことは、かえって企業の成長を止めることになることさえある。
在庫で何が問題なのかと言えば、無関心いる事である。
常に、企業のビジョンや目標に対して、どの水準にあるべきかを検討し、必要に応じてKPIを設定しPDCAを回していくことが大切だと考える。
朝活100本ノック /生産計画・在庫管理改革:75日目【在庫最適化とシミュレーション:安全在庫】
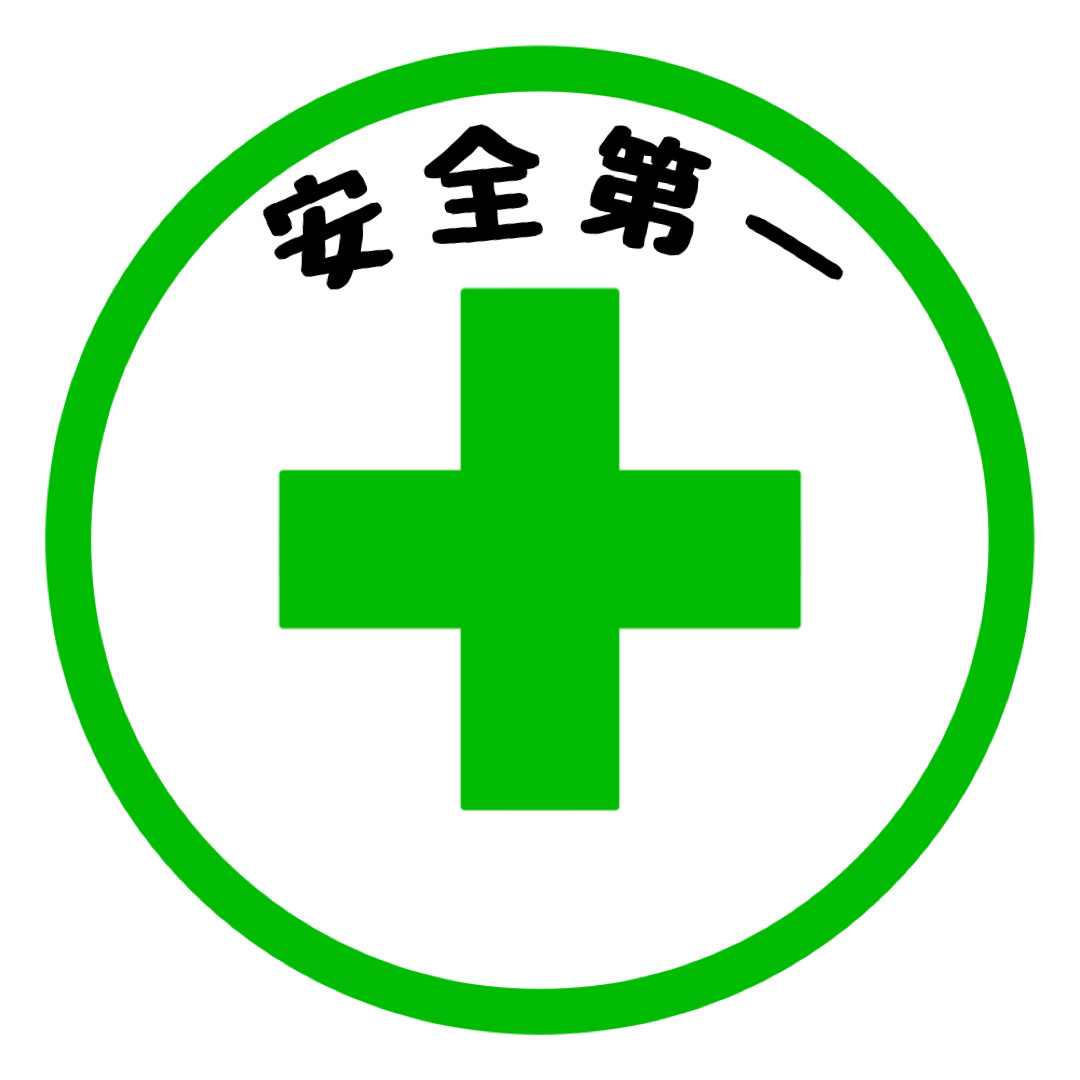
供給されるまでのリードタイム間に発生する需要のばらつきをまかなうために保持する在庫
安全在庫の削減対策
1、顧客との需要情報の共有
2、需要のほうがコントロールできない状況ではリードタイム短縮
ロットサイズ在庫、見越し在庫、安全在庫の他に、以下の分類があるする
④管理精度在庫:サプライチェーンの観点から、見える化や管理精度に起因して止まっている在庫(迷子になっている時間相当)
⑤デカップリング在庫:ブルウィップ効果に伴い発生
朝活100本ノック /生産計画・在庫管理改革:74日目【在庫最適化とシミュレーション:見越し在庫】
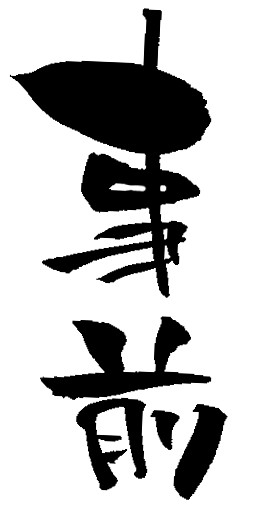
需要が供給能力を超え、供給能力不足に備えて、積み上げる在庫。
需要のピークに合わせて生産能力を保持すると整備投資が大きくなることを避けるため。
見越し在庫の削減
・需要の異なる季節変動パターンをも品目で組合せて供給側の負荷の平準化
・季節変動パターンの予測精度を上げることである。
朝活100本ノック /生産計画・在庫管理改革:73日目【在庫最適化とシミュレーション】
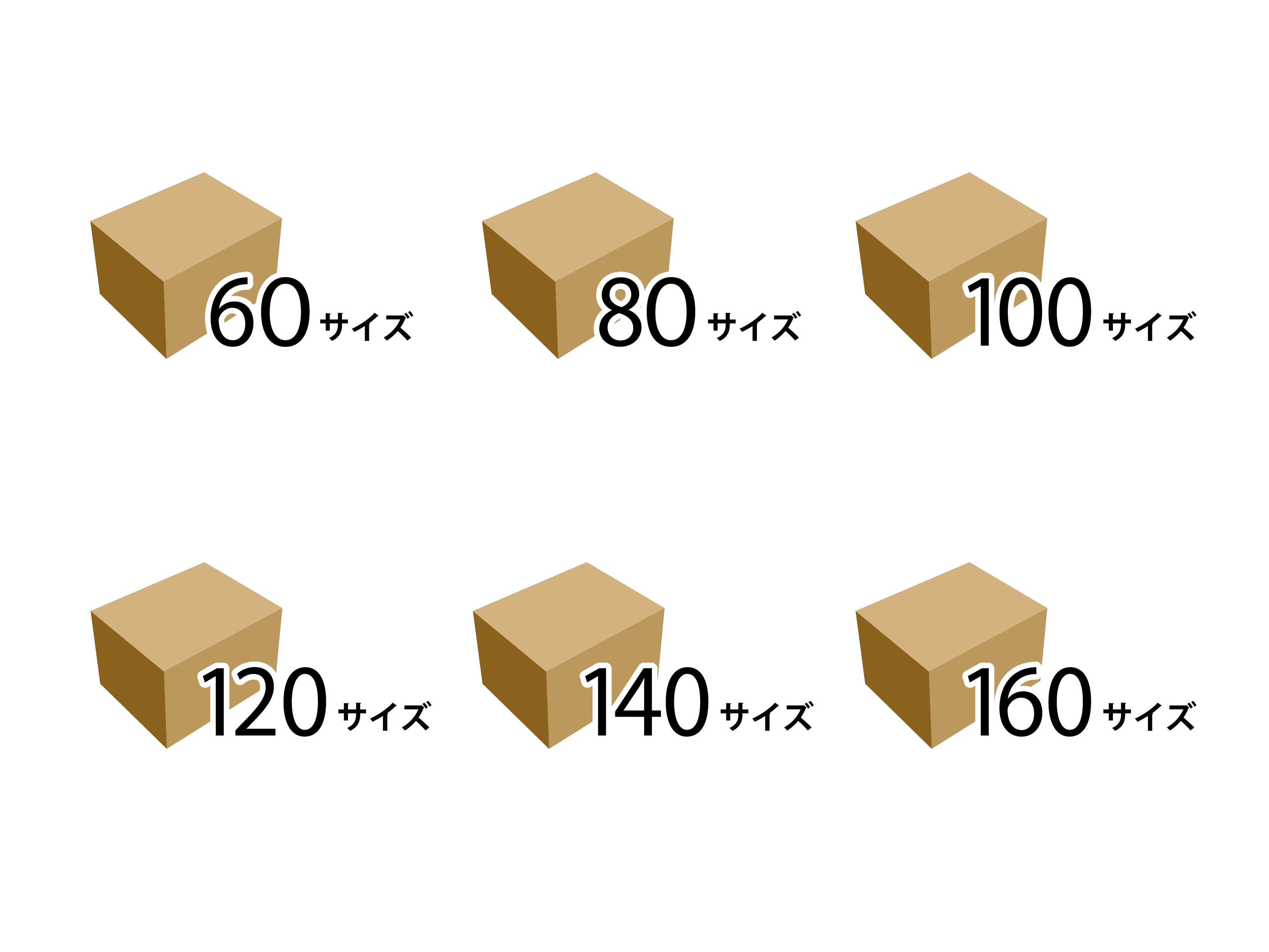
〇発生原因別在庫の分類
サプライチェーンが上手にコントロール=在庫が適正にコントロール
直接的に在庫を最適化するための基本ロジックについて解説
在庫はいろんな形態で、あらゆるところに存在する。そこでまずは、発生原因別、あるいは在庫を必要とする理由にもとづく在庫の分類と、削減のための着眼点を簡単まとめます
また、市場価格の変動を予測して、低価格のときに大量に購入し残存した在庫を『買いつなぎ(ヘッジ)在庫』と呼ぶ場合がある。
朝活100本ノック /生産計画・在庫管理改革:72日目【サプライチェーンの必要在庫のサイクルタイム半減効果】
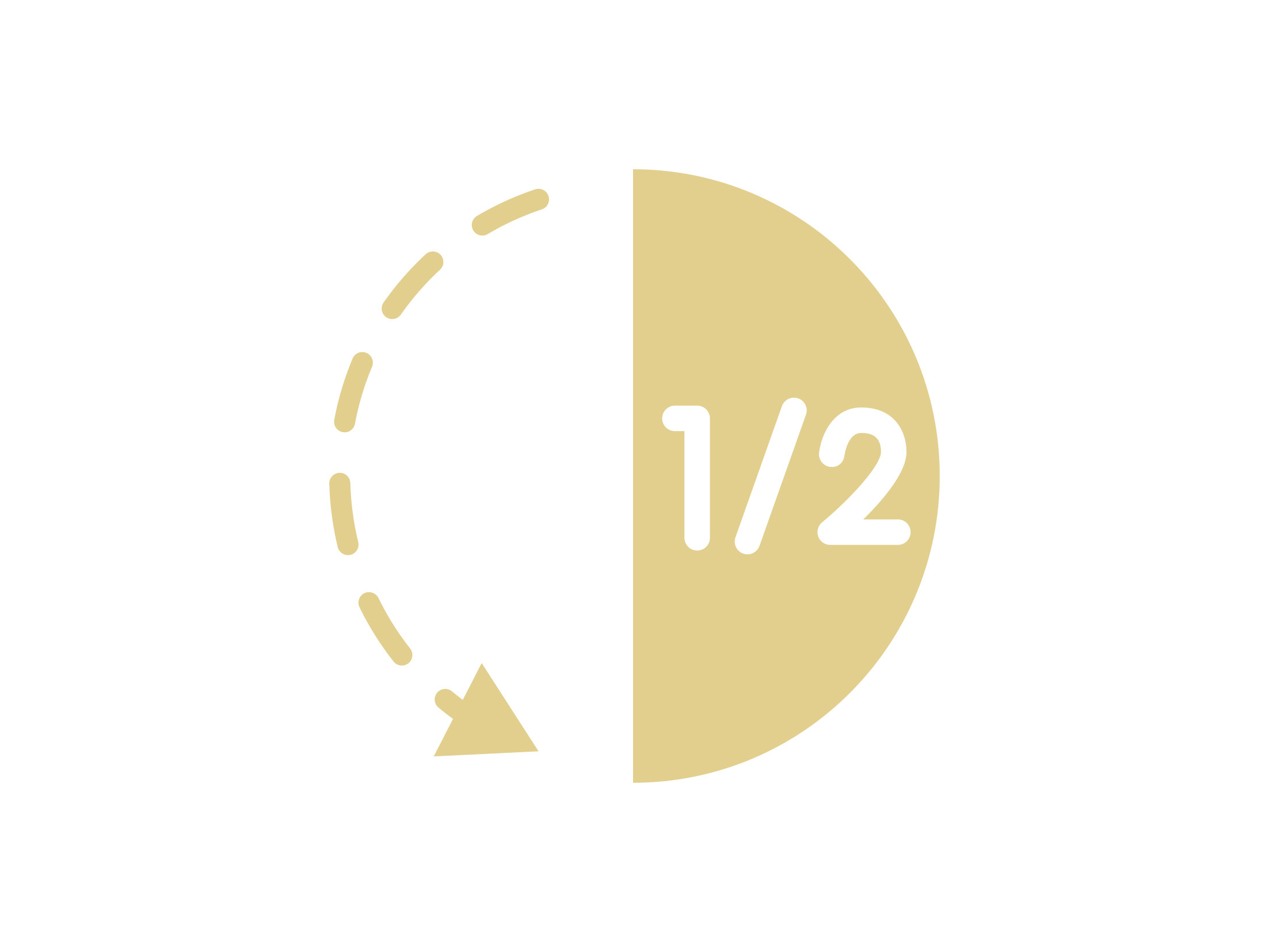
「ボトルネック」は、サイクルタイムに左右され、結果的に、顧客リードタイムは、サイクルで決まる場合が多い。メーカーの補充リードタイムは4日であったが、生産サイクルは200個の生産ロットに対して、日当たりの需要は平均10個で20日という生産サイクルとなる。この生産サイクルを20日から10日に半減した結果が、表中の数値となる。
情報共有しない『伝言ゲーム型』であっても、必要在庫は130個と半減以上になり、『情報共有型』よりも小さくなる。
内なるボトルネックである生産サイクルをいかに短縮できるかが、在庫量には大きく影響を及ぼすことが理解できる結果である。