インフォメーション
朝活100本ノック /生産計画・在庫管理改革:43日目【生産スケジューラ導入失敗要因は】
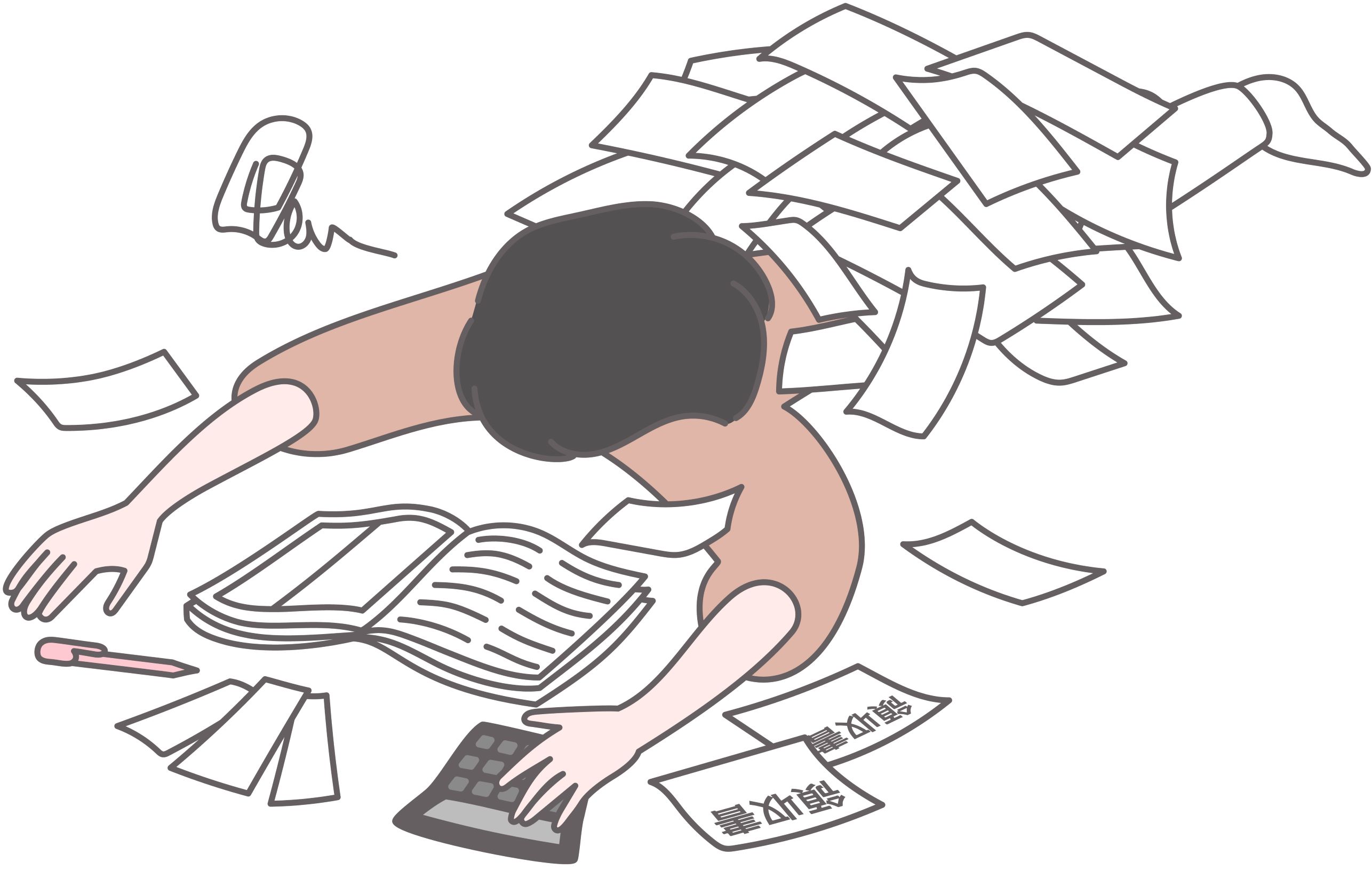
生産スケジューラの導入で、失敗が多いのは、主要業務以外を生産スケジューラで対応使用した場合である
スケジューラとは、
・予め登録したマスターから自動で山積み山崩しを実施し、工程単位で作業計画を立案
・専任の生産計画担当者が緻密な計画を作るためのツール
生産スケジューラは、計画を立案することに特化しており、生産計画担当者が苦労している
営業部門や工場(工程)とのやり取りを精緻化するシステムではない点を理解しなければならない
生産計画業務だからと言って、生産スケジューラを入れても、効果が出ないことになる
朝活100本ノック /生産計画・在庫管理改革:42日目【デカップリング・ポイントの運用】
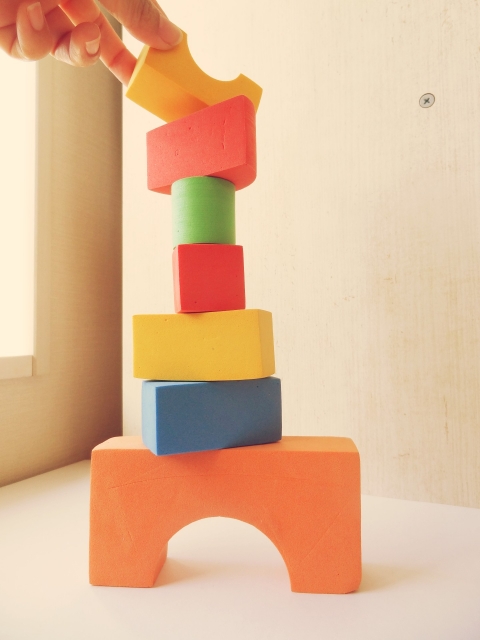
デカップリング・ポイントには、需要変動などの外的要因のため在庫を持つ必要があります。
在庫の持ち方には、主に3つのパターンが考えられます。
①安全在庫:適正在庫量や発注点を決定し、一定の在庫水準を維持する
②先行日数:リードタイム分など一定期間分に必要となる量をあらかじめ先行して在庫する
③安全需要:販売計画や直近の販売実績に、安全分を加味した数量にする。
デカップリングポイントの運用例
トヨタの自動車のMTO(受注生産)の為在庫は持たない運用です。
ただこれは、顧客が納期を待ってくれるため、実施が可能と言えます。
デルはBTOで飛躍した企業です。
Dellのパソコンは以前は、店頭で販売されていたSTO(販売在庫)でした
販売が不調になったところで、BTO(受注加工組立)に変更し大成功をおさめました。
DellのBTOは、部品だけを事前に在庫しておき、注文がきたら組み立てを行う方式でした。
Dell運用の特徴
製品在庫から部品在庫にすることによって、製品在庫の保管費用や売れないモデルの陳腐化を減らす事が出来ました。
経費の節減につながり、価格を安く抑える事にも成功しました。
倉庫費用、廃却予定費用(売れない金額をあらかじめ製品の折り込んでいる)などを大幅に減らし、経費が少なくなりました。
その分を、お客様に還元(価格を安くする)しました。これが受けて、デルは業績を回復させました。
業態やお客様の状況によって、運用を検討することはもちろん、会社としての戦略も含めて運用を決定しないと効果につながらないばかりか
逆に運用を悪化させてしまう結果にもなりかねません。
朝活100本ノック /生産計画・在庫管理改革:41日目【デカップリングポイント特徴と決め方】
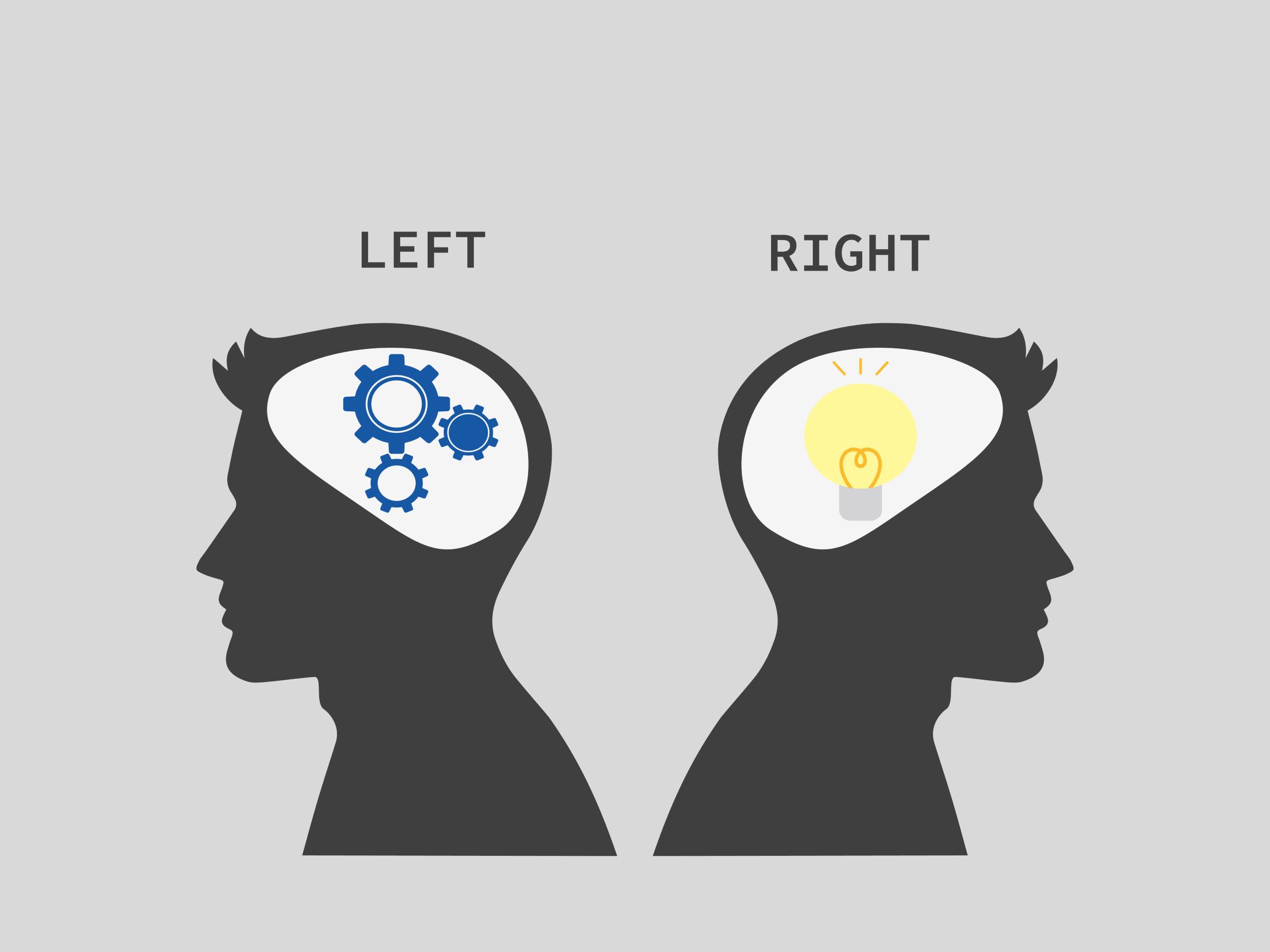
デカップリング・ポイントの決め方
1.販売の特性、工程、在庫品の共通性や性質から決める
・リードタイム(販売リードタイムと生産リードタイム)
・共通性(原材料や工程の共通性や保管のしやすさなど)
・使用(賞味)期限
2.計画とその後の受注実績で決定する
・事業計画(長期)で、予め出荷計画を決定する
・見込み生産(計画生産)で、販売計画に基づき、生産を計画する
・確定受注が入れば、在庫と紐づけて、販売計画を実績値に置き換える
・受注と紐づいていない在庫が溜まったところがデカップリングポイントとなる
朝活100本ノック /生産計画・在庫管理改革:40日目【デカップリングポイントとは】
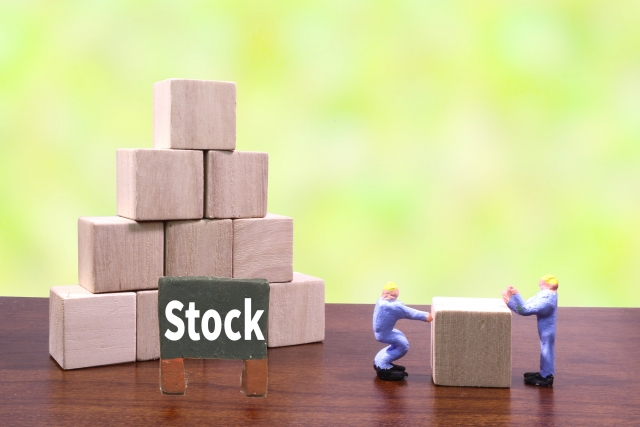
デカップリングポイント
(decoupling point)⇒「別ける」「引き離す」という意味
サプライチェーンマネジメントでいうと受注生産と見込生産の分岐点です
受注やサプライヤーなど外からの変動がサプライチェーンの上流に向かって、押し寄せる波を在庫を持つこで吸収・切り離すポイントです
サプライチェーンのどこかでバッファとしてデカップリングポイントを設定することも重要な施策となります
朝活100本ノック /生産計画・在庫管理改革:39日目【PULL生産方式とPUSH生産方式の混在】
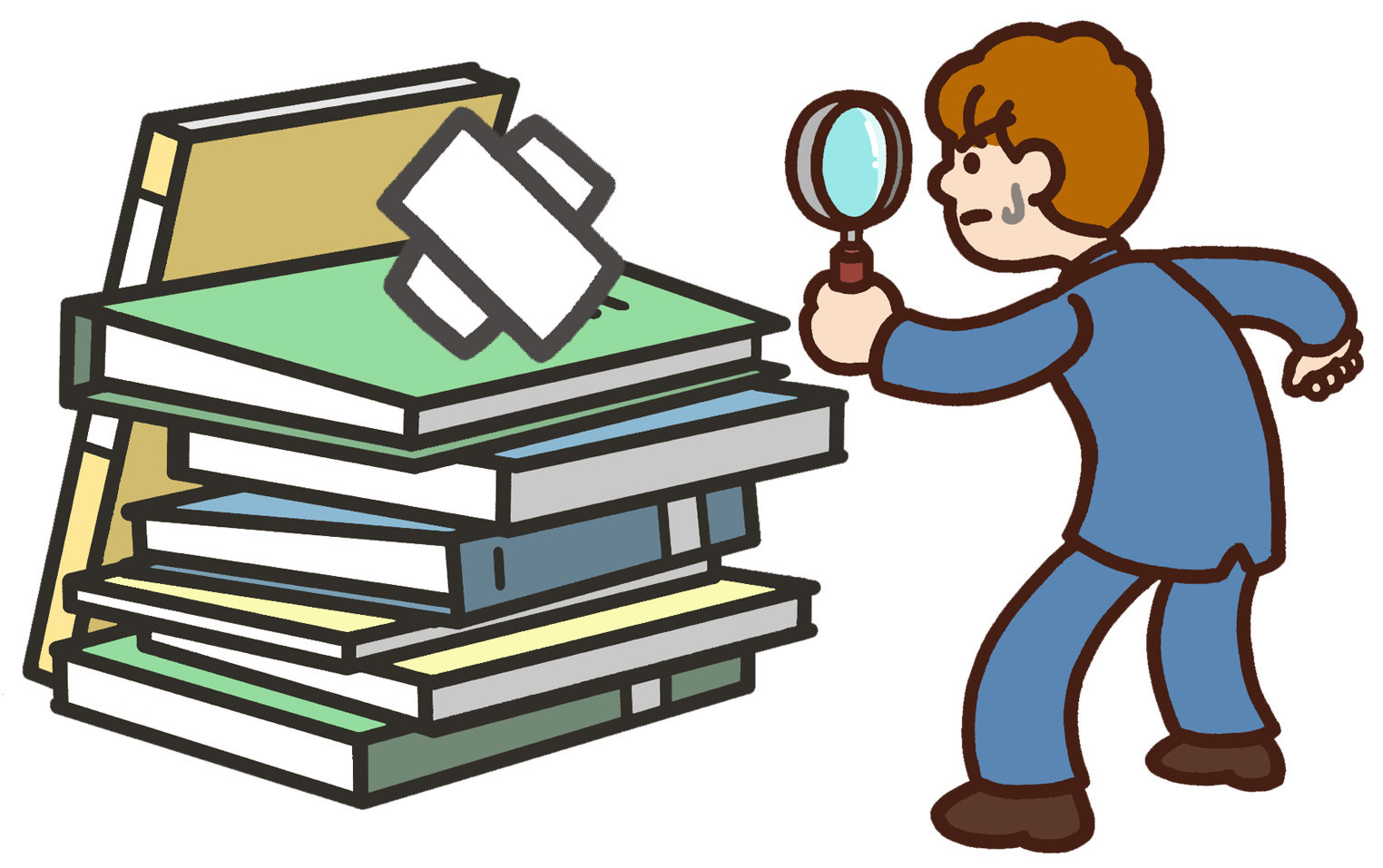
☆課題例
【在庫戦略:PULL生産方式とPUSH生産方式のコンフリクト】
1、発注点管理(PULL)の生産指示の対応が追い付かず、欠品や過剰在庫を招く。生産管理担当者は毎日バタバタしている
⇒発注点管理(PULL)を使用するのであれば、前工程の仕掛のバッファー設定が必要。正しく設定できないとバタバタした対応になり、対策が後手に回る
2、発注点管理(PULL)であるが、在庫責任が前工程(生産管理)になってしまい、拠点の適正在庫管理(正しい発注点)が出来ていない
⇒PULL生産方式は在庫責任が営業側になるのが通常です。発注の出発部門で適正在庫管理と発注点を作る事で正しい運用となります。