インフォメーション
朝活100本ノック /生産計画・在庫管理改革:62日目【需要予測が外れる前提のPDCA】
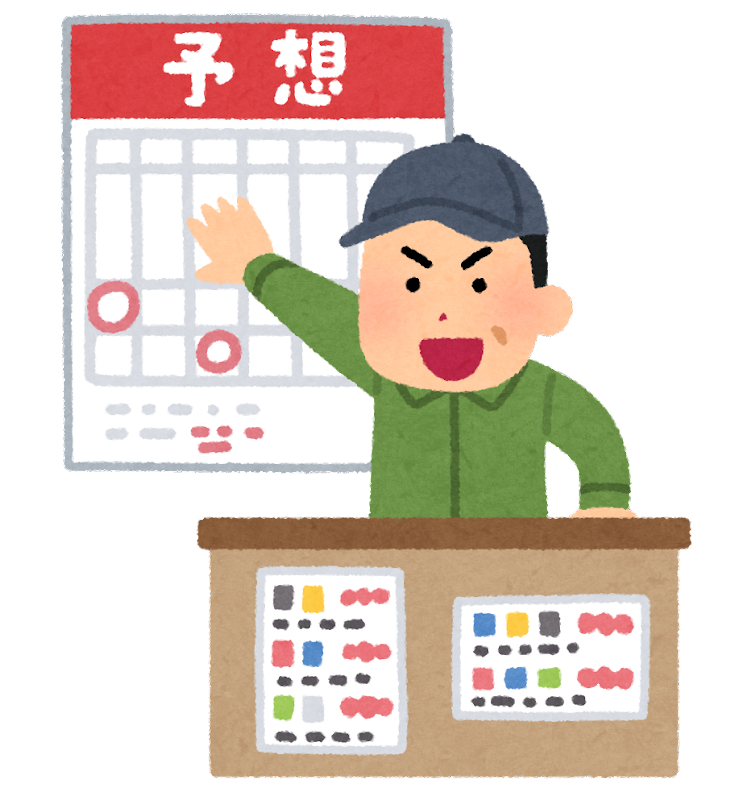
①あらかじめ予想が外れてても問題が生じないように、安全在庫による欠品への対策など対応しておく。
②以前示した予測誤差から安全在庫量を算出。
③安全在庫量の見直しは、Checkで予測誤差が過大、過小に偏る場合に、Actionで予測モデル自体の見直しを実施する。
また、需要予測が下降し、不動在庫となる可能性がある製品に対して、生産や販売の中止を検討することもPDCAサイクルを運用する重要な取り組みとなる。限られた在庫スペースに売れない製品があるために、売れる製品の生産に影響が出たり、不必要に倉庫を賃貸したりする事なる。常に回転する在庫を適切に管理し、収益性を高めていく必要がある。
朝活100本ノック /生産計画・在庫管理改革:61日目【需給マネジメント】
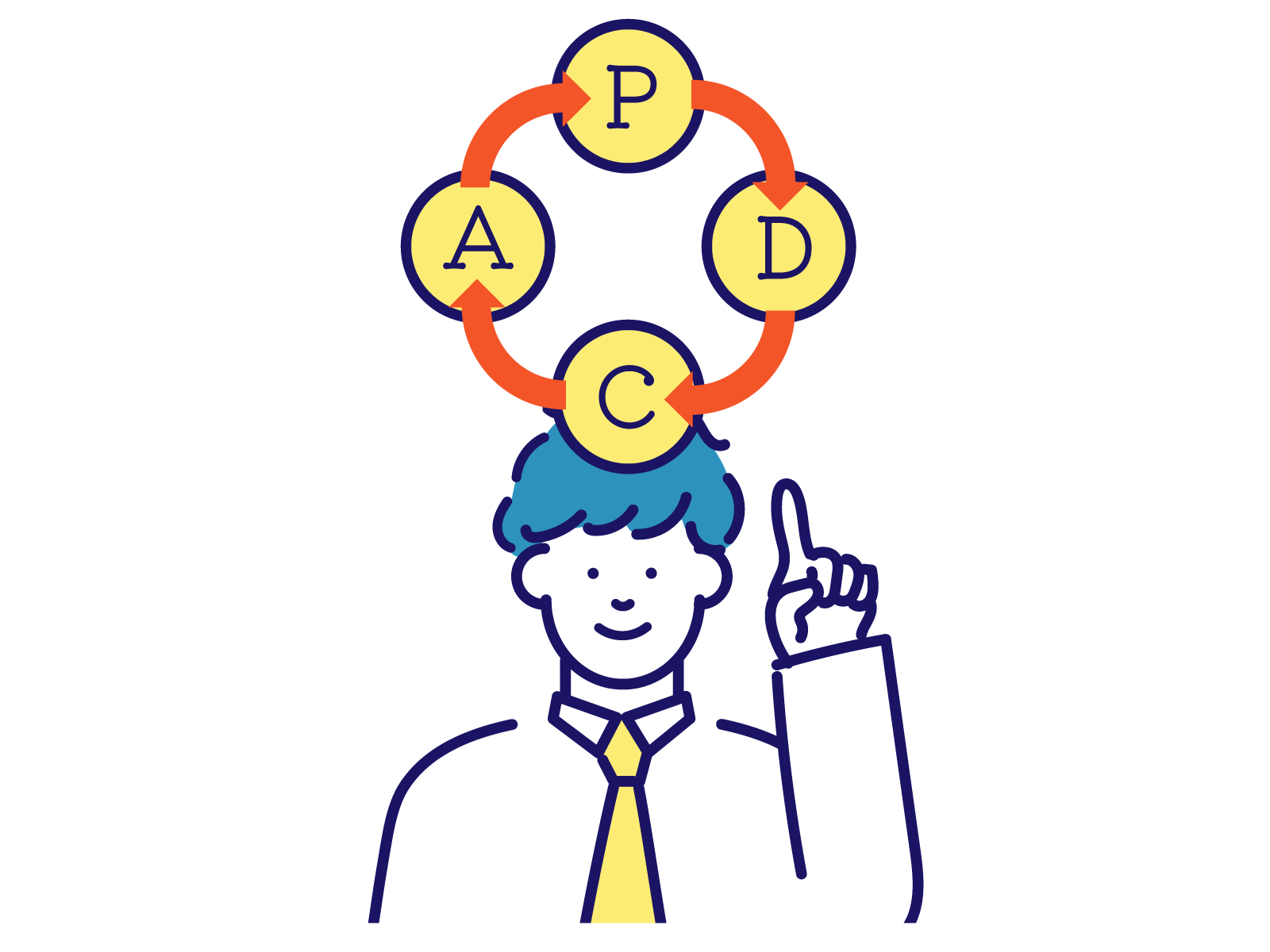
需要予測を適切に実施し、販売機会損失の削減や在庫の削減、廃棄ロスの削減、さらには生産計画などの見直しの抑制を図っていくためには、継続的な需要予測の改善が必要である。そのために、PDCAサイクルを実践する仕組みづくりが重要であり、3つのPDCAがあるとしている。
①予測精度改善のPDCA
②予測の外れを前提としたPDCA
③緊急対応のPDCA
最初に、①予測精度改善のPDCAについて説明
①予測精度改善のPDCA
予測精度を継続的に向上させるためにPDCAサイクルを回していく必要がある。
1、Planでは熟練者の経験と直感に頼っていた予測⇒予測モデルを用いた予測業務に変更、継続的な改善のためには属人化を排除し、業務の標準化を図る。
2、需要予測にもとづき、生産計画の策定
3、Checkにおいて問題が発見されれば、
4、具体的に何を改善するればよいかActをとることが可能となる。
☆仕組みつくり例
・季節性の予測が反映されていなく過剰在庫になったり、販促による特売が考慮されず欠品となったのであれば、それらの情報を予測に反映させる仕組みづくりを検討すればよい。
・Checkにおいては予測誤差を何千、何万もの商品一つずつ確認し、評価し問題の有無を判断するするのは難しい。一定以上の数値以上を警告とするルールを作成しておくなどがある。
・販売の実績データには欠品による失注の情報は含まれておらず、本来の需要量は厳密にはわからない。予測モデルを構築するために使用する実績データも注意がある。状況に応じて予測値を情報修正して真の需要に近づける活動が必要である。
朝活100本ノック /生産計画・在庫管理改革:60日目【メーカーにおける生産計画と在庫管理能力】
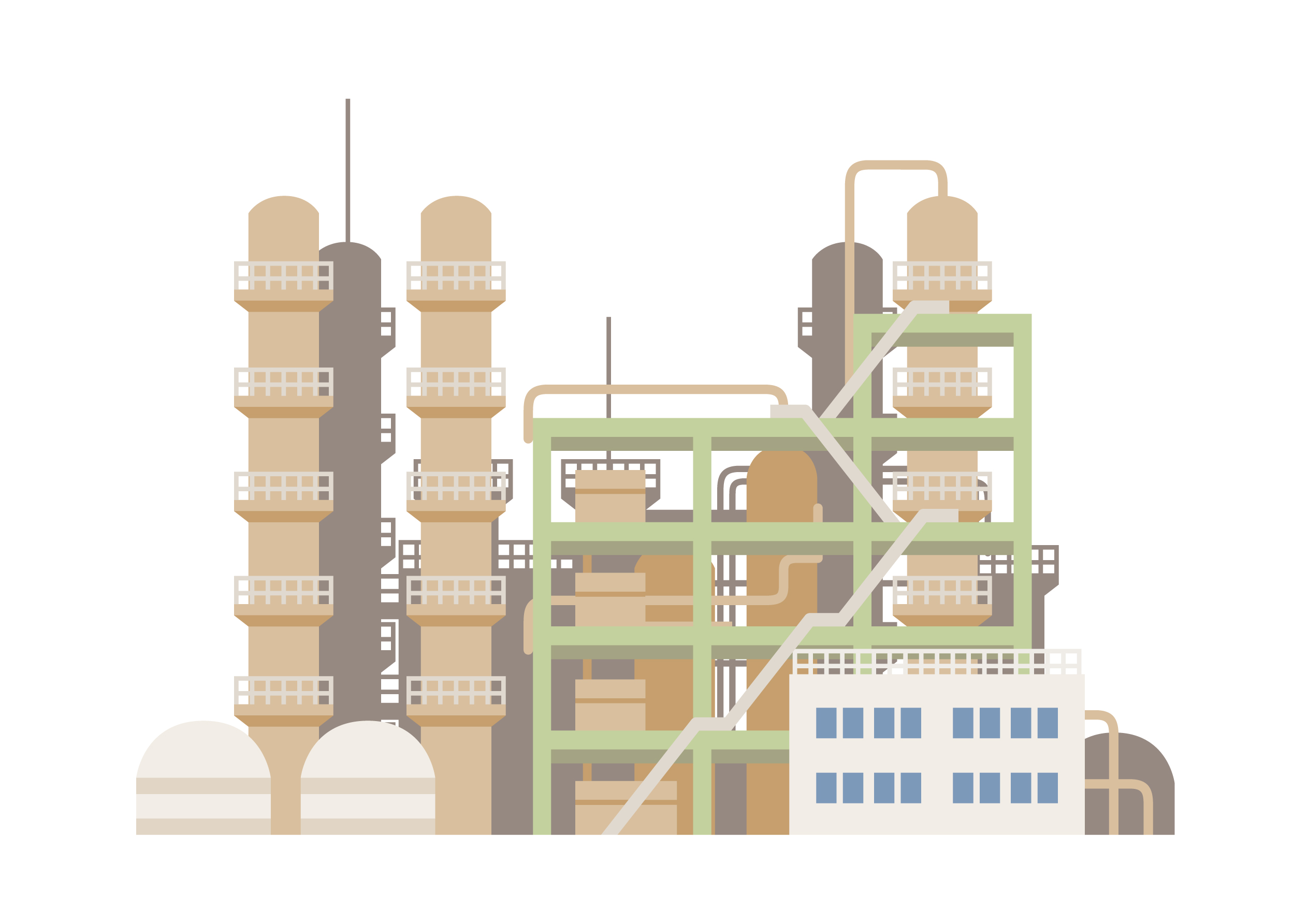
日々の発注に対応した生産を目指す為、通常は生産に必要な原材料や部品の調達、設備の段取替えや作業員の状況について検討する。そして、必要な期間(3ヵ月や1ヵ月)の需要予測を実施し、それにもとづいた販売計画を立案し生産計画のインプットデータとなる
ここで需要予測の結果を直接、生産計画に用いないのは、販促におけるイベントの実施や商品の改版や新製品の投入といった過去のデータからは予測できない値を踏まえた数値にもとづいた生産をする必要がある
一つの大きな例としては、2008年のリーマンショックの影響にいる急激な需要の落ち込みの事例がある。急激な需要の変化に対応するためには、生産計画の見直しサイクルが重要である。3ヵ月間まったく生産計画を見直さないのと、1週間ごとに生産計画の見直しを行うのとでは、需要量の変化に対する対応が大きく異なる
下図は、リーマンショック(2008年)の自動車メーカーの在庫の変動を表したものである。図中の横軸は四半期の在庫回転期間、縦軸は当期と翌四半期との在庫回転期間の差を示している。そして、記号内にある数値が、該当する四半期を表している
図から○社は、第1四半期から在庫管理基礎力が高く、在庫回転期間が他社より短い状態であった。その後、リーマンショックの影響により急激に需要が減少した際にも生産量をただちに調整したと考えられ、在庫回転率に大きな変動を与えていないことから、過剰な在庫を大量に抱えなかったと推察できる。このことから、○社は、需要の変化への対応力も高く、適切な在庫管理能力を有していると考えられる。
一方、△社や□社は、○社よりも在庫回転期間が長く、特に、在庫の変動が大きい、つまり、需要の変化への対応力が低いと考えられる。
現在は、スマートフォンの普及からSNSの利用が飛躍的に増加し、情報伝達が当時よりも速くなっている。したがって、特に消費財では需要の変動が激しくなっており、需要予測の精度を向上させるとともに、生産計画の見直し期間を短くし、需要の変化への対応力をたかめることが重要となっている。
生産計画の見直しを短サイクルで実行するためには、計画の修正に伴う部品調達(サプライヤーの協力)や作業員のシフト(製造ラインの協力)などの迅速に変更が行える体制を構築する必要がある。これらの体制が構築されれば、生産量を需要量に合わせて柔軟に調整することが可能となり、収益性の向上が望めるが、体制を構築しないまま短サイクルを実施すれば、生産計画担当者の負荷が増加するだけでなく、サプライヤーや製造ラインへの過度な負担を強いられたり、場合によっては、不必要な在庫が積み上がる結果となる。
朝活100本ノック /生産計画・在庫管理改革:58日目【卸売業や小売業対象の需要予測にもとづく在庫管理②】
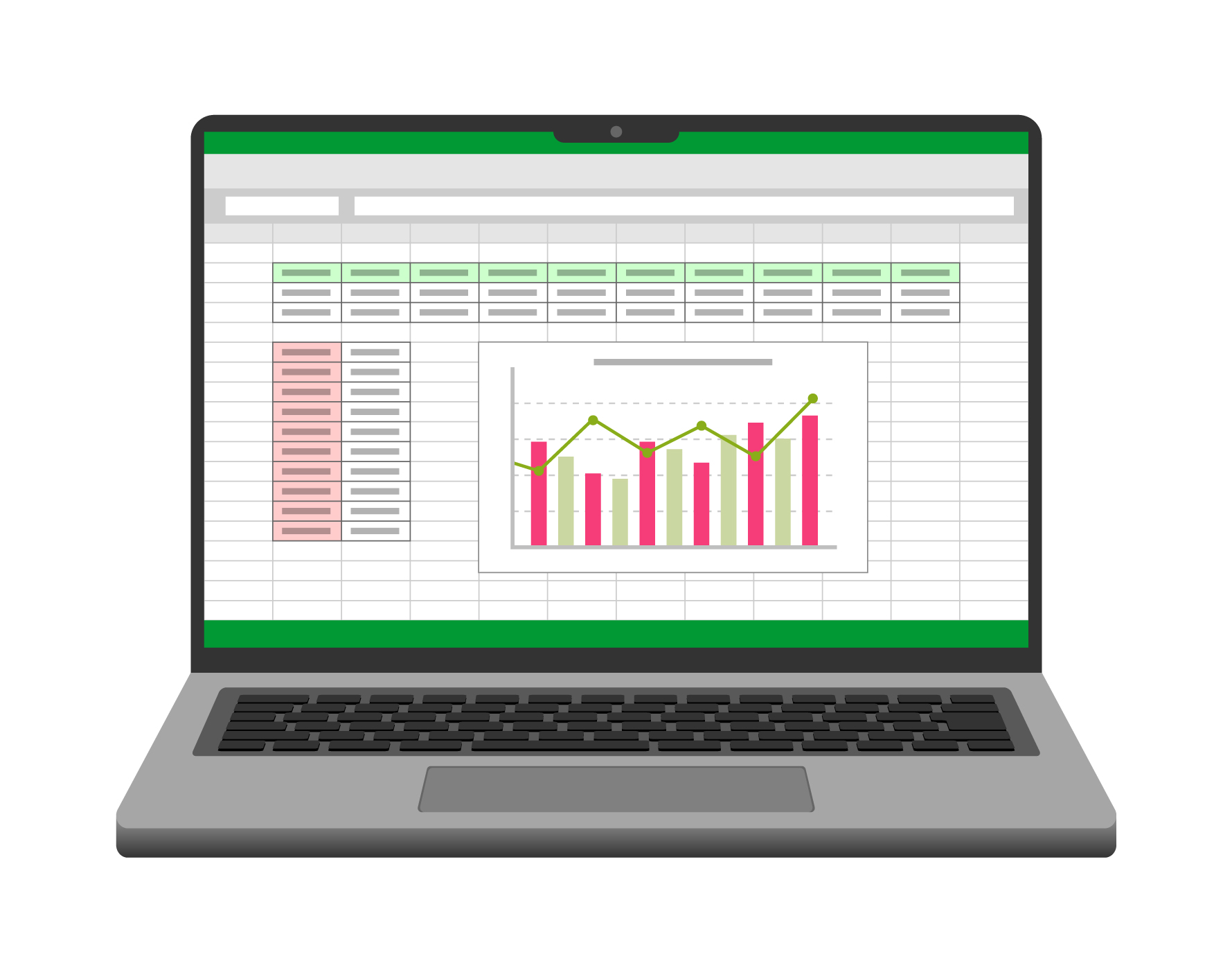
1、考慮すべき予測期間(A-D間)の需要量を予測する(移動平均法など)
2、需要予測値が実際の需要量と一致することは少なく、多くの場合は誤差が発生する
3、誤差を考慮した安全在庫量を加える必要がある
以上のことをまとめると、考慮すべき予測期間中の予測需要量は、次のように求めることができる
☆需要予測安全量の算出式(期間中の需要予測値+安全在庫量)
=期間中の予測値+安全係数(1.65)×考慮すべき予測期間(A-D間)×考慮すべき期間の使用量の標準偏差(過去の出荷量・販売量の平均値)
※安全在庫の計算方法
「安全係数(1.65)」×「使用量の標準偏差」× √(発注リードタイム+発注間隔)
※安全係数は欠品許容率を指し、一般的に欠品許容率5%にあたる1.65を使用
※使用量の標準偏差は過去の出荷量・販売量の平均値
また、在庫量を適切に保つために必要な発注量は、現在時点で保有している在庫量(発注残を含む)を予測需要量から差し引いた分となる
この場合の考慮すべき予測期間(A-D間:発注間隔+調達期間)を一定とした発注方式が定期発注方式で、代表的な発注方式である。ちなみに、この定期発注方式は商品ごとに予測モデルを構築する手間がかかることから、売上高の多い重要な商品に用いられ、ほかの商品にはより簡便な発注点法や二棚法が用いられることが多い
※二棚法:2つの棚に同じ在庫量を置き、片方の棚の在庫がなくなった時点で発注(補充)する在庫管理
在庫管理の主な方法は、定期発注方式、定量発注方式、二棚法があります
朝活100本ノック /生産計画・在庫管理改革:58日目【卸売業や小売業対象の需要予測にもとづく在庫管理】
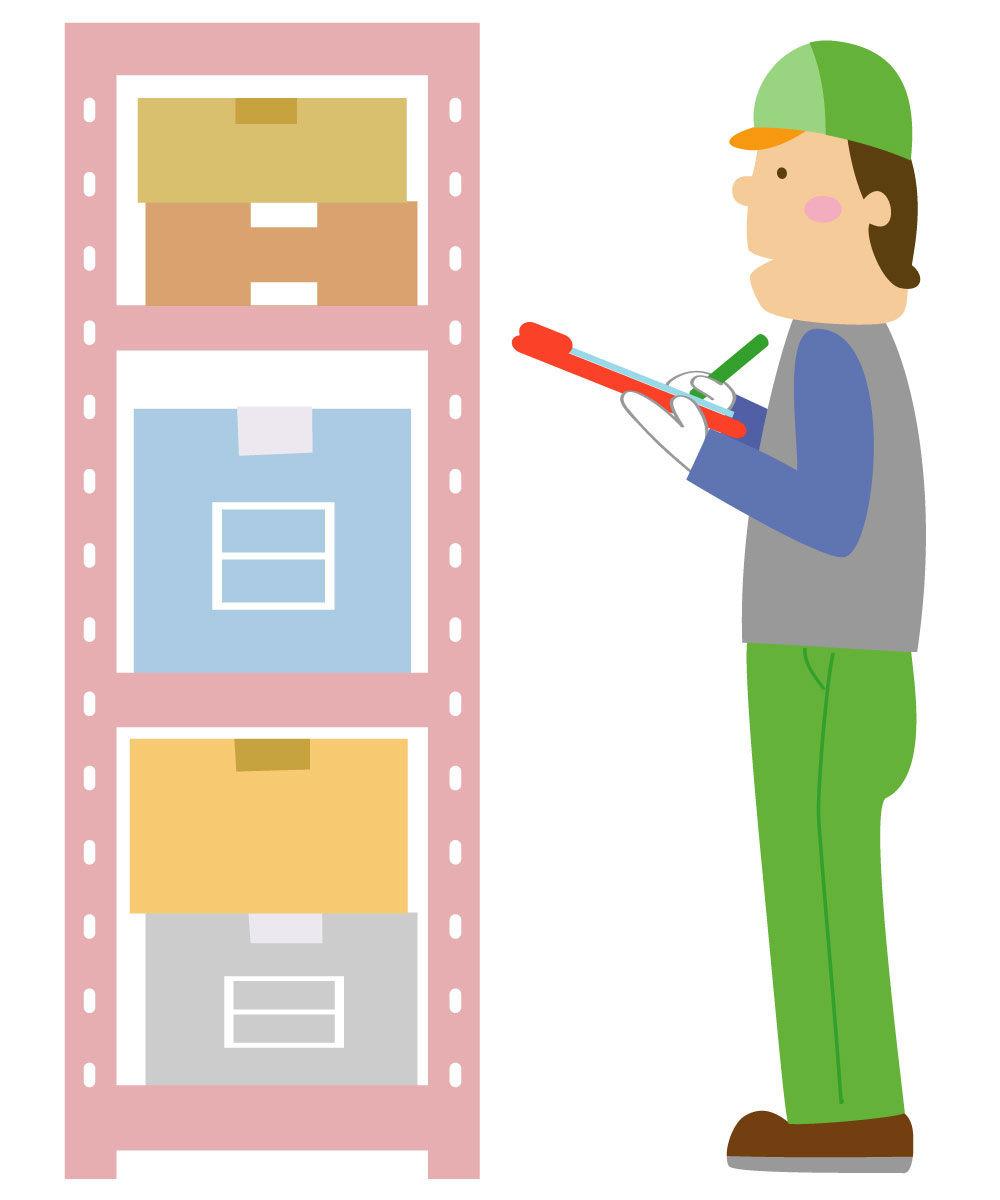
☆小売店での定期発注方式など需要予測から毎回の発注量を算出する例
1、現在(A)で、商品の発注
2、調達期間を経た後に店舗に入荷(B)⇒次回の発注から入荷までの時点(D)まで、店頭で販売
○発注の考慮期間とは
・販売期間(B-D間)(次回の入荷まで)に対応した 需要量を発注する必要がある
・現在時点(A)から次の入荷(B)までの調達期間(A-B間)の販売にも対応が必要である
⇒現在時点(A)の発注での考慮すべき予測期間は、A-D間となる(在庫起点)
また、発注起点で見ると現在から次回までの発注間隔(A-C間)と次回の調達期間(CーD間)を足し合わせた期間が必要である
○発注で考慮すべき予測期間(A-D間)の計算式は次の2つとなる
・現在の調達期間(AーB間)+現在考慮すべき販売期間(BーD間)
・現在から次回までの発注間隔(A-C間)+次回の調達期間(C-D間)